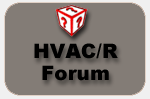 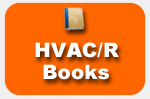
|
Northeast HVAC News Guest Column
Too small for supply chain
management?
By Howard W. Coleman, MCA Associates.
For the past 10 to 15 years, you
may have read about Fortune 500 companies undertaking Supply
Chain Management (SCM) initiatives. Business publications are
constantly reporting on the successes – the improved
profitability, the reduction in operating expense and the better
utilization of inventory.
A study done by The Performance Group of PRTM Consulting finds
that specific types of manufacturers with mature Supply Chain
practices are 40% more profitable than manufacturers with less
mature SCM practices.
Supply Chain Management is a set of cross functional processes
that allow for the efficient flow of product and the most
effective utilization of resources. SCM spans all movement of
materials and product inventory from point-of-origin to
point-of-consumption. SCM encompasses the planning and
management of all activities involved in sourcing, procurement,
manufacturing, distribution and logistics management activities.
Importantly, it also includes coordination and collaboration
with channel partners, which includes suppliers and customers.
In short, SCM integrates supply and demand management within and
across companies.
Most of the companies to date that have re-engineered their
processes and made large investments in SCM initiatives have
been multi-billion dollar multi-national corporations. They have
been able to add one more component to their quest for
“operational excellence”.
How Can This Work In Your
Distribution Business?
Let’s take a look – first at SCM, and then you.
SCM improvement initiatives usually focus on three pillars:
•Process – the steps/tasks required to efficiently execute a
specific function
•People – the skills and knowledge required to satisfy the
specific steps/tasks, including the education and training
needed to elevate and sustain performance as well as culture and
attitudes
•Technology - the tools that are necessary to support, enhance,
and measure performance
You have the same three! Aren’t these the same focus areas in
your company that dictate how effective, overall, your company
is - or will be?
Story
continues below ↓
advertisement
|
your
ad here
The above study also
states that there is a maturation process that should occur in your
company to optimize both the performance and the benefits of SCM. It
starts by recognizing that you are part of a “Supply Chain” and is
driven through your company by a “Lean Thinking” and a “Continuous
Improvement” process that needs to be part of your company’s culture
(visit our ?Web site for a copy of our article, “Lean Thinking In
Wholesale Distribution – Are You Ready For Little Miracles?”).
SCM through a “Lean Thinking - Continuous Improvement” process
addresses the following stages or elements:
1.Connectivity – how well are the internal and external business
functions communicating?
2.Collaboration – are the functions making decisions sequentially or
simultaneously?
3.Synchronization – does everyone know the same thing at the same
time?
4.Leverage – do you know where to focus on SCM to optimize
productivity and profitability?
5.Scalability – can you replicate processes from one function,
location, supplier, customer to another?
“Lean Thinking – Continuous Improvement” focuses on the tasks and
functions, as well as on the “people enhancement” required within
these stages to eliminate the non-valued-added steps that keep the
drive toward “operational excellence” alive.
Typically, these stages are addressed within a company first, and
then can be expanded to the company’s customers and suppliers.
Regardless of the channel, they require strategic, tactical and
operational level activities that have to do with:
•Strategic partnerships with suppliers and customers and creating
communication channels for critical information
•Informational technology infrastructure to support the supply chain
•Aligning overall organizational strategy and structure with demand
and supply strategy
•Customer relationship and supplier relationship management
•Sourcing, procurement and inventory decisions (quantity and
location)
•Coordinating your demand forecasting with customers and suppliers
•Order fulfillment and distribution operations planning and
execution
•Returns management
•Transportation operations and decisions
•Performance measurement (costs, customer service, productivity,
quality of services and asset measurement)
Industry organizations, such as NAED (National Association of
Electrical Distributors), have recently developed “Supply Chain
Scorecards, Benchmarks and Best Practices,” which through their
identification of the “Key Drivers” and components (efficiency,
performance measures and management measures) of supply chain
performance - are excellent. ASA (American Supply Association) and
NAW (National Association of Wholesale-Distributors) are all making
similar efforts.
Whether its electronic orders, vendor managed inventory, or new
on-line applications and informational content, in SCM there is also
a “discovery” of the metrics which will measure a process/function
the best and foster a constant focus on driving performance through
those metrics.
Now, Let’s Look At You
Chances are you’re trying to do this already, but maybe not in a
formal organized manner.
Your business has the same functions as a much larger corporation:
•Procurement
•Distribution Operations or Manufacturing Operations
•Inventory Management
•Sales and Marketing
•Financial Controls
•Delivery of “value-added services”
Each of these functions is made up of the same “pillars” – process,
people and technology.
Your questions may be the same as those larger companies that have
already been through these initiatives:
•Are we doing things the right way? Is it the most efficient?
•Is inventory being managed the same way by everyone, in a location,
or across locations?
•Are we getting product from suppliers and to customers in the most
efficient and responsive manner?
•What could we eliminate to decrease operating expense and
redundancy?
•What could we improve, without adding cost?
•Do I have the right people in the right process?
•Can my technology support my “lean thinking - continuous
improvements”?
See -You’re Not Too Small At All!
Your size gives you distinct advantages when looking at Supply Chain
improvements:
•You probably operate “lean” now, so getting to root-causes and
problem resolution will be faster.
•You are not spread across the country (or world!), so proximity and
accessibility allows changes to be implemented more quickly and
easily.
•Your Technology may be adequate – you just may need to utilize it
differently. If so,
•You can focus on the Process and People pillars which will yield
the most dramatic results
The time is right! SCM and “Lean Thinking – Continuous Improvement”
processes have been refined and pretty much standardized. The
methods to get people involved - inside and outside your
organization - the required training of the concepts, and the
implementation activities required, has been tested and proven.
So take advantage of all the ground work that has been done so you
can quickly become one of the more profitable companies - in the
next study!
Howard Coleman is the principal of MCA Associates, a management
consulting firm since 1986. MCA works with wholesale distribution
and manufacturing clients that are committed to seeking operational
excellence. MCA Senior Consultants provide idea leadership and
implement continuous improvement solutions focused on business
process re-engineering, inventory and supply chain management, sales
development and revenue generation, information systems and
technology, organizational assessment and development, and
succession planning.
Contact: hcoleman@mcaassociates.com or 203-732-0603. Visit
www.mcaassociates.com.
###
|
|